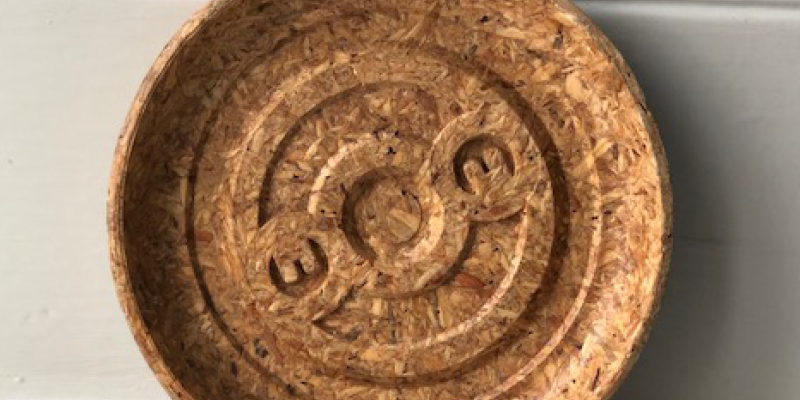
In this article, we will go in-depth with the material molded wood chip or particle.
The material is a composite material that is often used for structural seats or back parts in upholstered office chairs.
We believe this material has much unused potential as it is both very
- low cost
- effectively produced
- has a low footprint.
Its material properties and looks resemble chipboard and MDF. The molding process makes it possible to vary the material thickness only where it is needed. Material thickness can go down to 5mm thickness which makes it a great option for weight and cost reduction.
Compared to chipboard and MDF the footprint is approximately the same per kg, but by redesigning the part to the lower wall thickness and less weight considerably lower emissions can be obtained.
The molded wood chips are also a good option for material replacement of cast metal parts in case high strength and high humidity resistance are not needed. The material has less design freedom than cast metal parts have, so this should be taken into account when designing the part.
As a customer of our tool, you will receive precise guidelines on how to calculate the footprint of molded wood particle products and see how much the climate footprint can be reduced in comparison with conventional materials.
There are also new effective means of surface treatment that you can compare. It all depends on which surface finish you are aiming for.
The data in this article is subject to changes.