Antonio Scaffidi
furniture designer
Antonio Scaffidi is an experienced furniture designer and one of the founding members of Danish Design Makers.
A bio-based design
Antonio is comfortable with his brief. Maybe a little too comfortable, since he has decided to break with some of the requirements. He feels like challenging the company a little and inspire them with his material choices.
“They want a wooden product, an integrated design, and very high ergonomics. But that is somewhat ambiguous to me since wood needs a lot of processing to obtain high ergonomics and that requires a lot of energy and glue. From my perspective, that doesn’t go hand in hand with the reduction theme.”
Thus, Antonio is working with another bio-based material, which he has experimented with in the past. He hopes to obtain flexibility in this material and thus make the design more lively than it would have been if it was only made of wood. Though he cannot simulate this factor beforehand.
I find it exciting to work with new, innovative materials. But it is also a bit unnerving, because I don’t know the durability of this product before I actually make the prototype.”
Antonio thinks of an integrated design as being a design where the elements fit well together and meet each other in an elegant way. He wants to show this off in his design by assembling all parts with screws in a visible manner.
“I want my product to be easily taken apart, so I am designing for disassembly. This is to prolong the product lifetime as each part can be disassembled for repairing or replacement. Normally, the places where materials meet in a product are hidden away, but I want to show how easy it is to disassemble my design. I think it is a very honest way to handle this design expression.”
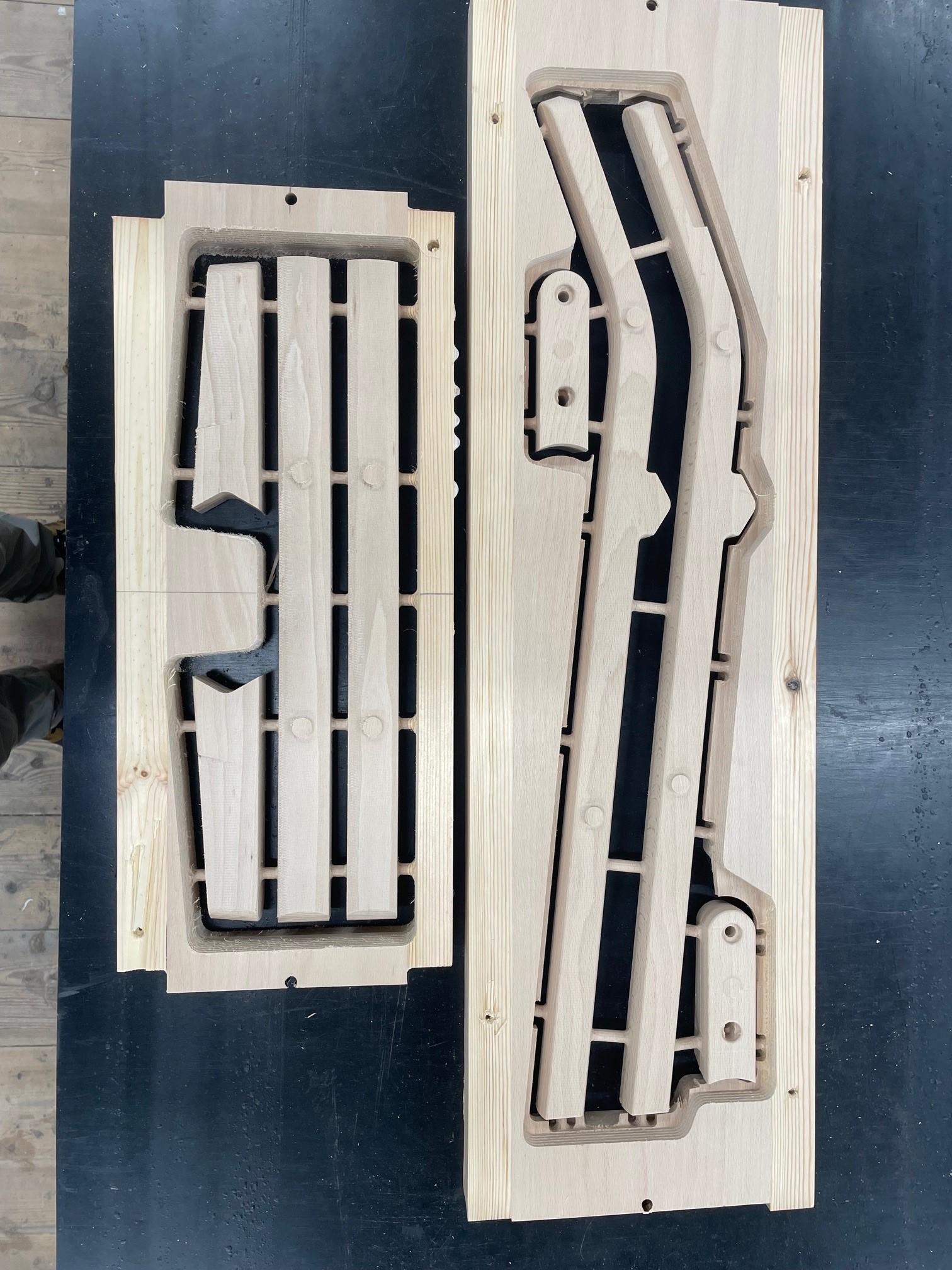

New materials are often unfit to be tested by current industry standards
“I don’t think my design will live up to the conventional test requirements for the contract market”
Antonio stresses that it requires a willingness from the industry to embrace the new alternatives to fossil materials. A transition to more bio-based materials also requires the safety tests, durability tests, and hygiene tests to evolve, because new materials do not necessarily fit into existing standards.
If we want to change the industry for the better, we need to reevaluate our current way of doing things and I believe this involves reassessing the conventional test and certifying requirements. I think this project set-up is a fine opportunity for Danish Design Makers to have such discussions with the industry”.
It is indeed a shame if too many innovative projects using new materials stop because traditional test requirements are outdated. But we also need to think about what will and can happen to these new materials that are invented. Can they be recycled? Can they be composted? Or will they just end up as unusable trash because we lack processing systems for them?
Participants are unbiased
Antonio finds the blind date experiment interesting because both designers and companies are unbiased. The designers only need to deal with their task at hand and accept that they must wait for the companies’ reactions and feedback. The companies also take a chance not knowing the designers and their work in advance.
“I am very curious to learn what happens when we meet the companies at the fair. Everyone should be. I don’t think anyone has tried this set-up before.”
This designer is optimistic about the reveal and looks forward to this important meeting with the industry.
This article reflects the designer’s own opinion and Målbar does not necessarily agree with their statements about materials, processes, etc.
Climate calculations and insights
Antonio has made two versions of his bio-based chair; one with armrest and one without.
The one with an armrest has a total estimated climate impact of 22 kg of CO2eq.
The one without an armrest has an estimated total climate footprint of 21 kg of CO2eq.
The attempt to minimize manufacturing by choosing low emission manufacturing technologies and low emitting materials has provided meaningful emission savings.
The choice of primarily biobased materials in comparison to fossil based does not necessarily decrease the emissions. Many bioplastics have high emissions from manufacturing and the decomposition of biomaterials in an average European scenario where it ends up at landfills emits methane gas. This result may surprise some who believes that biomaterials are always a better choice. It is a bit complex because the total emissions of biobased bio-degradable materials rely very much on how the material ends its life. If it is being deposited on a landfill, it will result in high methane emissions. But if it ends its life being incinerated, the biobased carbon emitted (in CO2) is not counted and it also provides heat energy. All in all a benefit for the climate. This means that the footprint will change a lot depending on how the particular country handle its waste.
The strategy to avoid glue is not entirely carried through as melted PLA-fiber is used to glue the flax fibers together. The high amount of PLA raises the emissions.
Even though the chair is stackable with 4 pcs per box, its transport emissions are noticeable. This is because despite being stackable, the volume of the 4 chairs is still rather high.
The chair emissions have the potential to become even lower by careful selection of material alternatives, such as a less emitting glue.
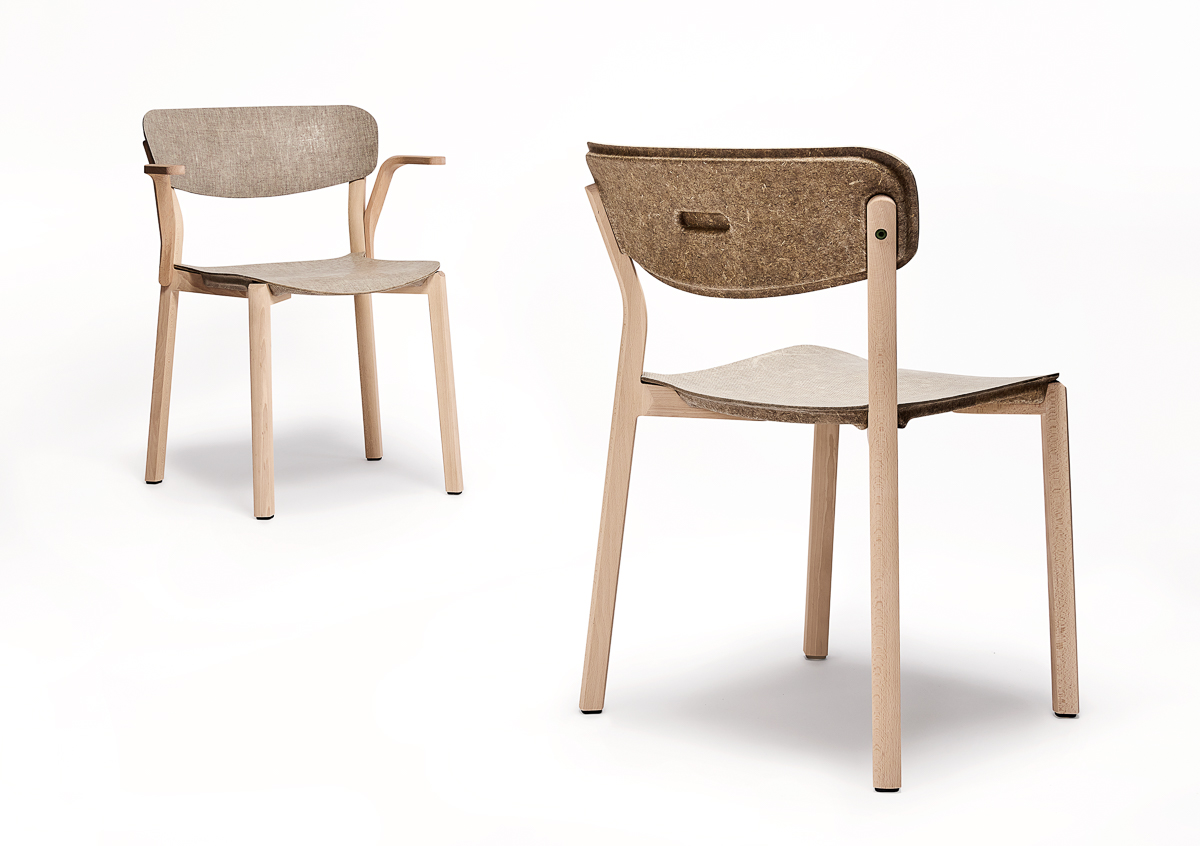
Photo by Kristine Funch
Explanation of climate bar
The climate bar shows how the emissions from the design are distributed between 10 sources within the product life cycle. Here you can see that a major part of the climate impact comes from transport. Second, the production phase takes up a significant part of the emissions. This is due to the manufacturing of the bio composite that is used for the seat and backrest. Finally, it is worth mentioning the cover, which makes up for almost 25% of the footprint. Here, it is the flax and PLA that the bio composite consists of.
There are emissions from the use phase on all products, because of the waste that is generated from returned products from consumers.
Assumptions
- The amount of manufacturing waste of solid wood is assumed the same as the amount used
- Actual amounts of textile bat manufacturing waste have been calculated
- Average amounts of 15% textile cover manufacturing waste have been added
- We assume that metals, plastics and textiles are produced according to the global average unless we know differently. All other materials are assumed to be produced in the EU
- We assume a transport distance by lorry from supplier to warehouse of 1,000 km
- We assume a transport distance from warehouse to final client of 1,000 km
Målbar builds their assumptions on their experience with industrial production and LCA’s on manufacturing companies.
Context
Målbar participates in Danish Design Makers’ 2024 design challenge, The Blind Date experiment where 19 designers and design duos answer furniture briefs from anonymous European furniture companies. The designers use Målbar’s climate screening tool to gain insigths into the climate emissions of materials and production processes, learning about the climate impact of their design choices. Ultimately, the total climate footprint of each design will be calculated and presented at ORGATEC in Cologne on October 22nd-25th 2024.