Thomas Sigsgaard
furniture designer
Thomas Sigsgaard is part of the renowned design duo Salto & Sigsgaard and has been a member of Danish Design Makers for many years. He graduated from The Royal Academy of fine arts in 1995.
A design process is a tool
Thomas always finds it interesting to receive a brief revealing his task. And he thinks this task is relevant and that the company has made their wishes quite clear.
Thomas always approaches a design task the same anthropological way. He thinks of his design process as a tool.
The task varies from time to time, but my way of designing is always the same. Apart from the fact that I get a little better every time, and my methods are sharpened over time.”
First, Thomas engages in a research process to gather all information about what may influence the product before he starts shaping his design. Then he finds a design concept. And after that he tests his idea.
“I’m not going to present a design set in stone. I wish to be flexible towards the company, so they can contribute to the design with their experience and knowledge. To me, the most important thing is the principle or the concept of the design.”
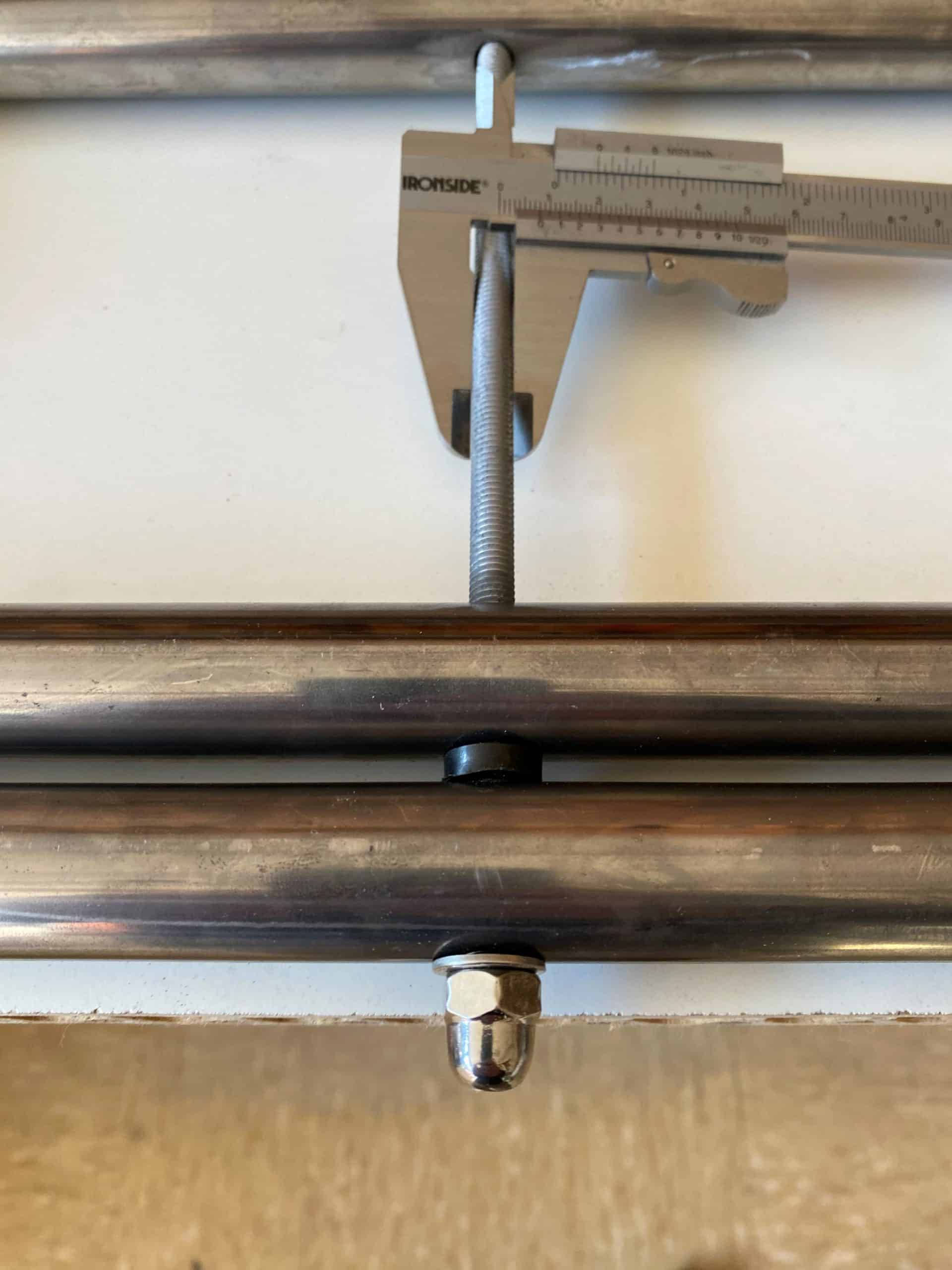
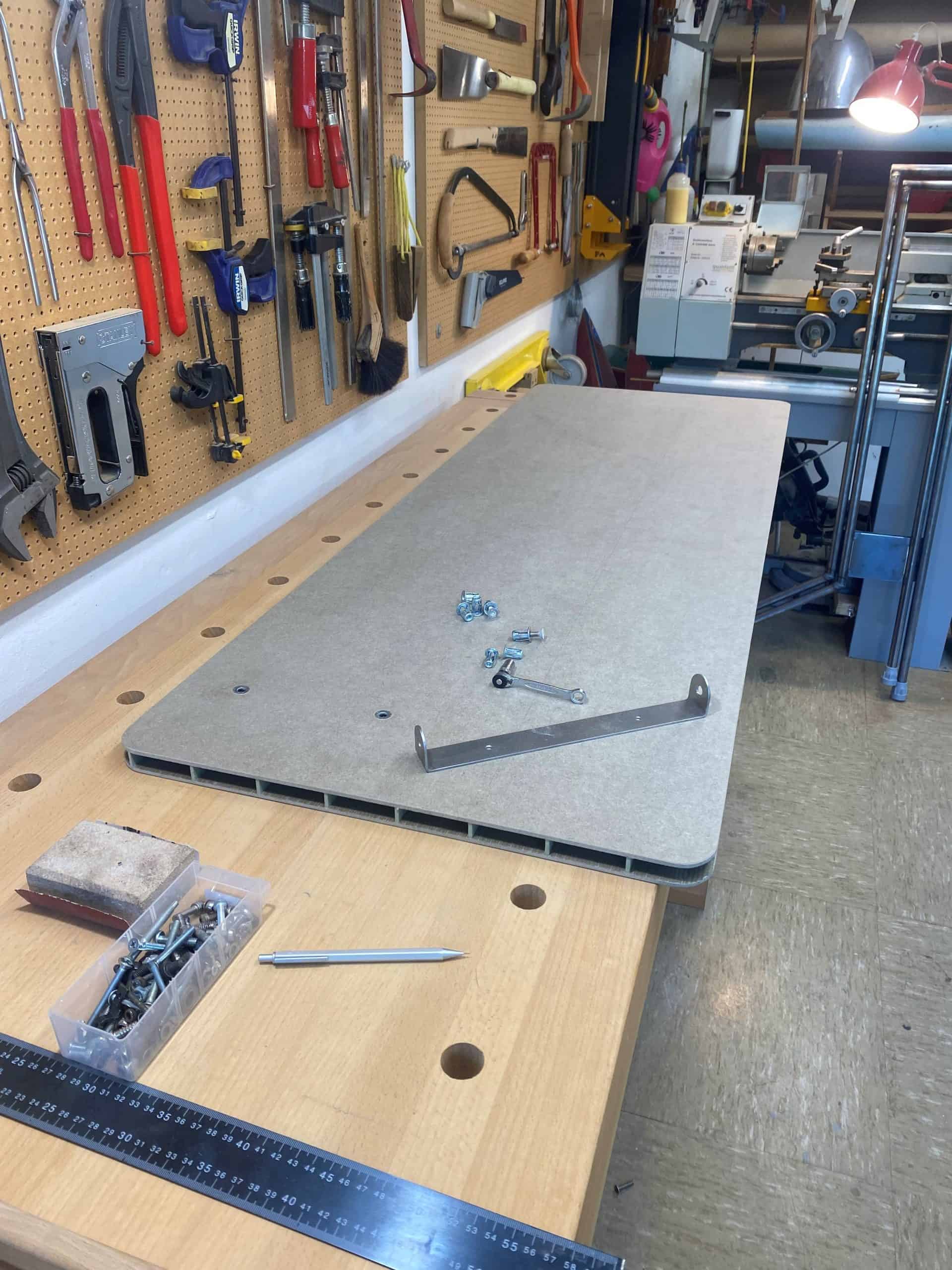
Blind dating is challenging
The main challenge for Thomas in this otherwise fun experiment is that he can’t align his idea with the company and benefit from their expertise before he makes it. He doesn’t want to make a lot of guesses, so instead, he has concentrated on fine tuning his concept.
It’s not that I’m worried they don’t like the expression of my design. It’s being prevented from co-deciding whether this piece of furniture has a justification in the world. We should in fact always ask, what does the world need?”
Thomas has always appreciated the opportunity to create designs that solve problems. He like to invent. To him, designing is about making something that is capable of cracking real-life challenges. Then it doesn’t matter much what material the product is made of, as long as it is durable and long-lasting.
Designing isn’t sustainable
According to Thomas, no matter what we create, it isn’t sustainable to produce stuff. So, what’s the next best? For him, it is to make something that the world needs.
“This is what I’m trying to do. I’m trying to create something that currently doesn’t exist. And I think it would be unwise to exclude specific materials solely because of their climate emissions if these materials are needed to solve the problem.”
In spite of this, Thomas likes the Målbar tool. He finds it interesting to see the difference in emissions between two materials that have almost the same characteristics. Thomas looks at his own design process as being democratic and open to inputs, and he has considered and worked with the insights he has gained from working with Målbar.
This article reflects the designer’s own opinion and Målbar does not necessarily agree with their statements about materials, processes, etc.
Climate calculations and insights
Thomas has named his adjustable worktable Lift. It is inspired by the classic ironing table and has an estimated total climate footprint of 55 kg of CO2eq.
Thomas has succeeded in reducing the weight of his tabletop by using an open-structured board. The climate reductions following the weight reductions are based on our estimates as we have not been able to get information on the production of this specific board. However, if replaced with a typical 18 mm thick tabletop in MDF it would weigh around 6 kg more and increase emissions by 44%.
The choice of avoiding a motorized lift mechanism by making a mechanical hand adjusted table has been very effective in reducing emissions since the table won’t use electricity in its use phase contrary to most other height adjustable work desks.
These calculations are based on the design prototype which is manufactured without surface treatment. Therefore, emissions are expected to rise if surface treatment is added.
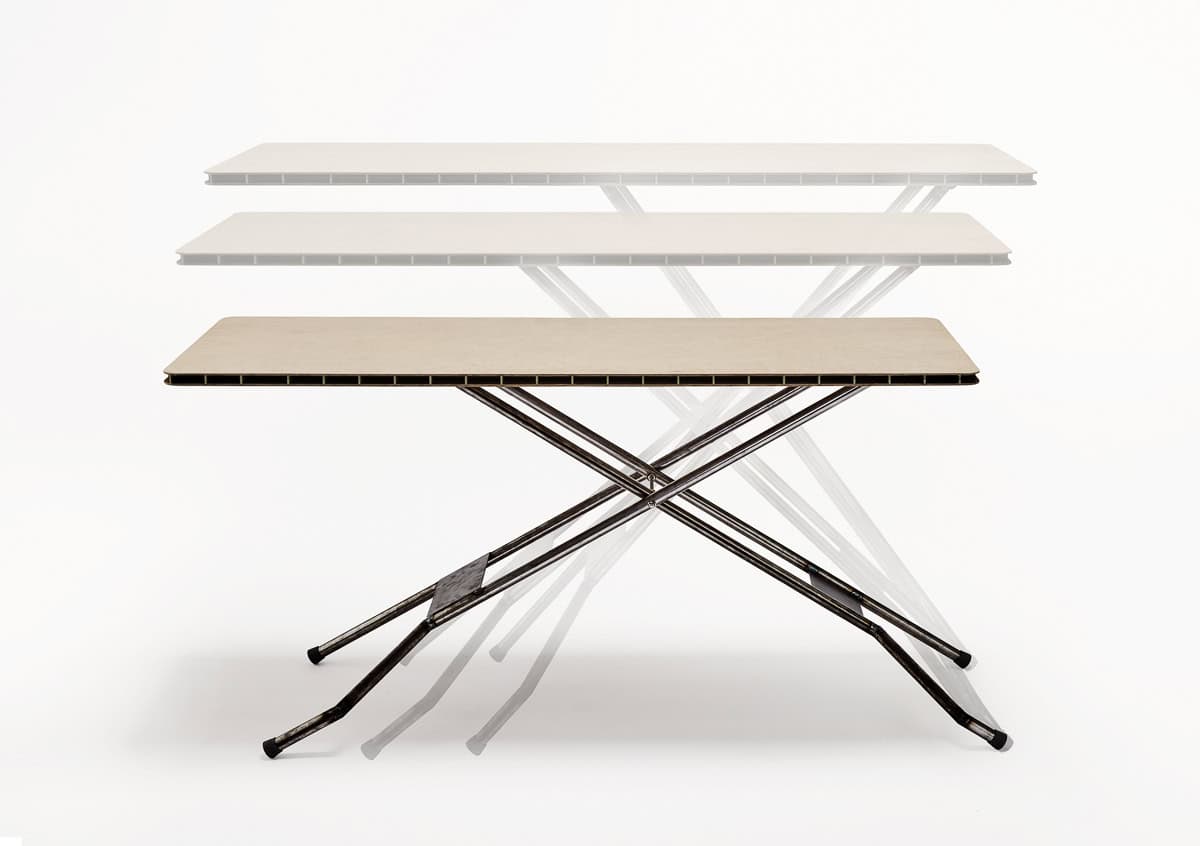
Photo by Kristine Funch
Explanation of climate bar
The climate bar shows how the emissions from the design are distributed between 10 sources within the product life cycle. Here you can see that the biggest impact stems from the materials, in this case the metals. However, there is also a noticeable part of the climate bar below zero, which means that 8.6 kg of CO2eq are detracted from the final result. This illustrates the credit given for having designed the metal parts for recycling at end of life by making the component easy to be disassembled from the rest of the materials.
There are emissions from the use phase on all products, because of the waste that is generated from returned products from consumers.
Assumptions
- It has not been possible to obtain lifecycle data on the specific open structured MDF board. Therefore, Målbar has estimated this. The cutting waste of the specific open structured MDF board is calculated according to the dimensions of the raw boards
- For metal tube manufacturing, waste of 10% has been assumed
- We assume that metals, plastics and textiles are produced according to the global average unless we know differently. All other materials are assumed to be produced in the EU
- We assume a transport distance by lorry from supplier to warehouse of 1,000 km
- We assume a transport distance from warehouse to final client of 1,000 km
Målbar builds their assumptions on their experience with industrial production and LCA’s on manufacturing companies.
Context
Målbar participates in Danish Design Makers’ 2024 design challenge, The Blind Date experiment where 19 designers and design duos answer furniture briefs from anonymous European furniture companies. The designers use Målbar’s climate screening tool to gain insigths into the climate emissions of materials and production processes, learning about the climate impact of their design choices. Ultimately, the total climate footprint of each design will be calculated and presented at ORGATEC in Cologne on October 22nd-25th 2024.