Troels Flensted, exhibition
and conceptual designer
Troels Flensted graduated from Central Saint Martins in London in 2014 and founded his studio in Copenhagen in 2015. This is his second time exhibiting with Danish Design Makers.
Inspired by materials
Troels is an experimental designer who works conceptually with objects. Usually, he begins his design process by being inspired by a material or a process. He then examines it to learn how it can be used in new ways to create different expressions. Troels creates unique furniture for exhibitions and gallery settings.
For this project, Troels had almost from the beginning decided to work with a new type of surface coating made from worn out and recycled textile fibers. Luckily, this material fitted well with his brief.
The brief is quite open, but also expresses clear guidelines. They want an organic shape, which I think is interesting to work with and which I see it as a good basis for creating a shape that offers different ways of seating”
Troels is building for differently shaped modules that can be combined in many ways. They are to be coated with the textile fiber surface coating that he believes is an interesting way to work with textile recycling and a cool way to coat surfaces.
Through his organic shapes, Troels works to create a design that invites different ways of sitting and being in or on the furniture. With his decision to make three modules, he goes beyond the brief’s wish for a lounge chair and creates a sofa-like design that can be turned into a chair if the middle piece is taken out.
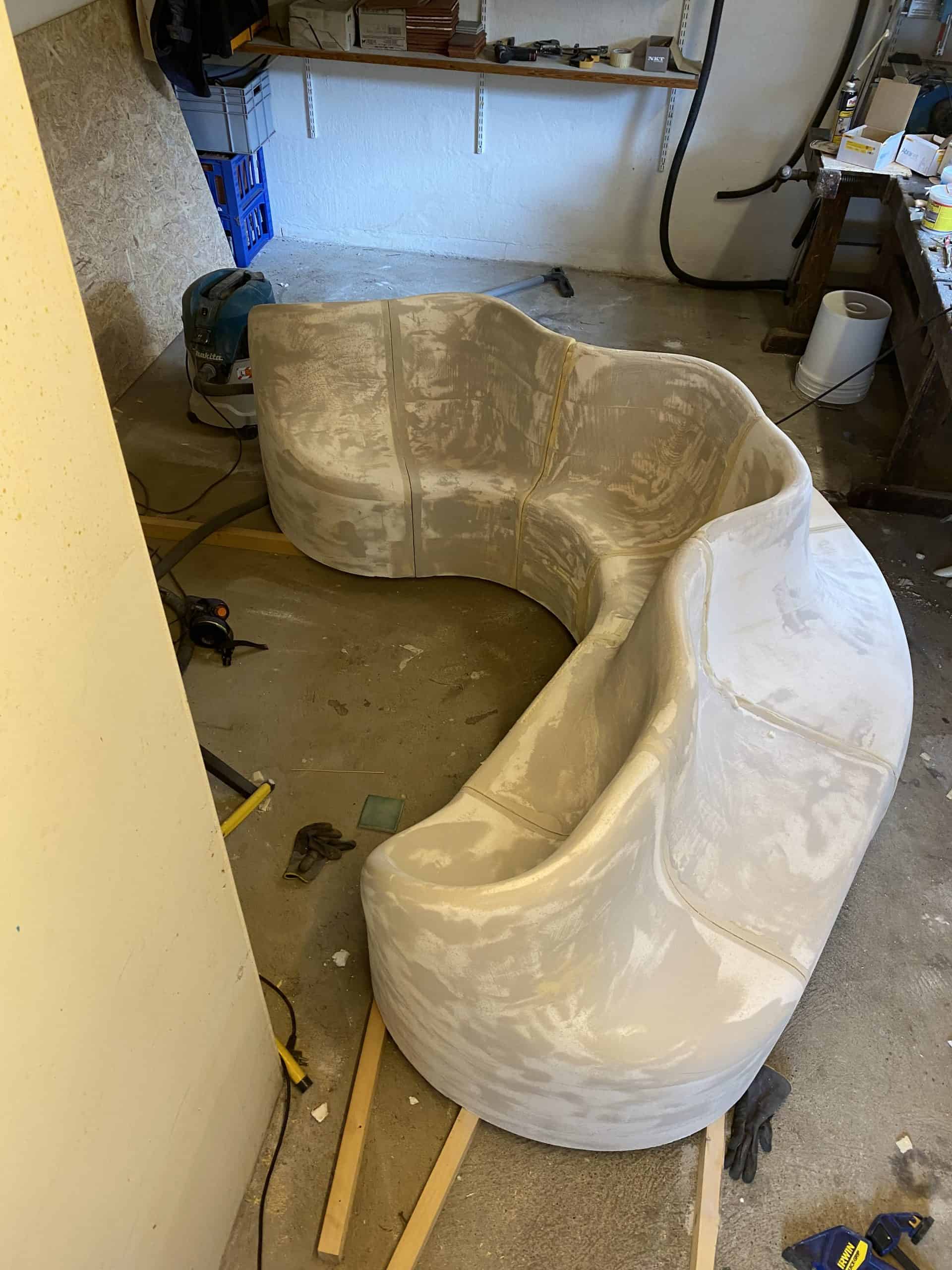
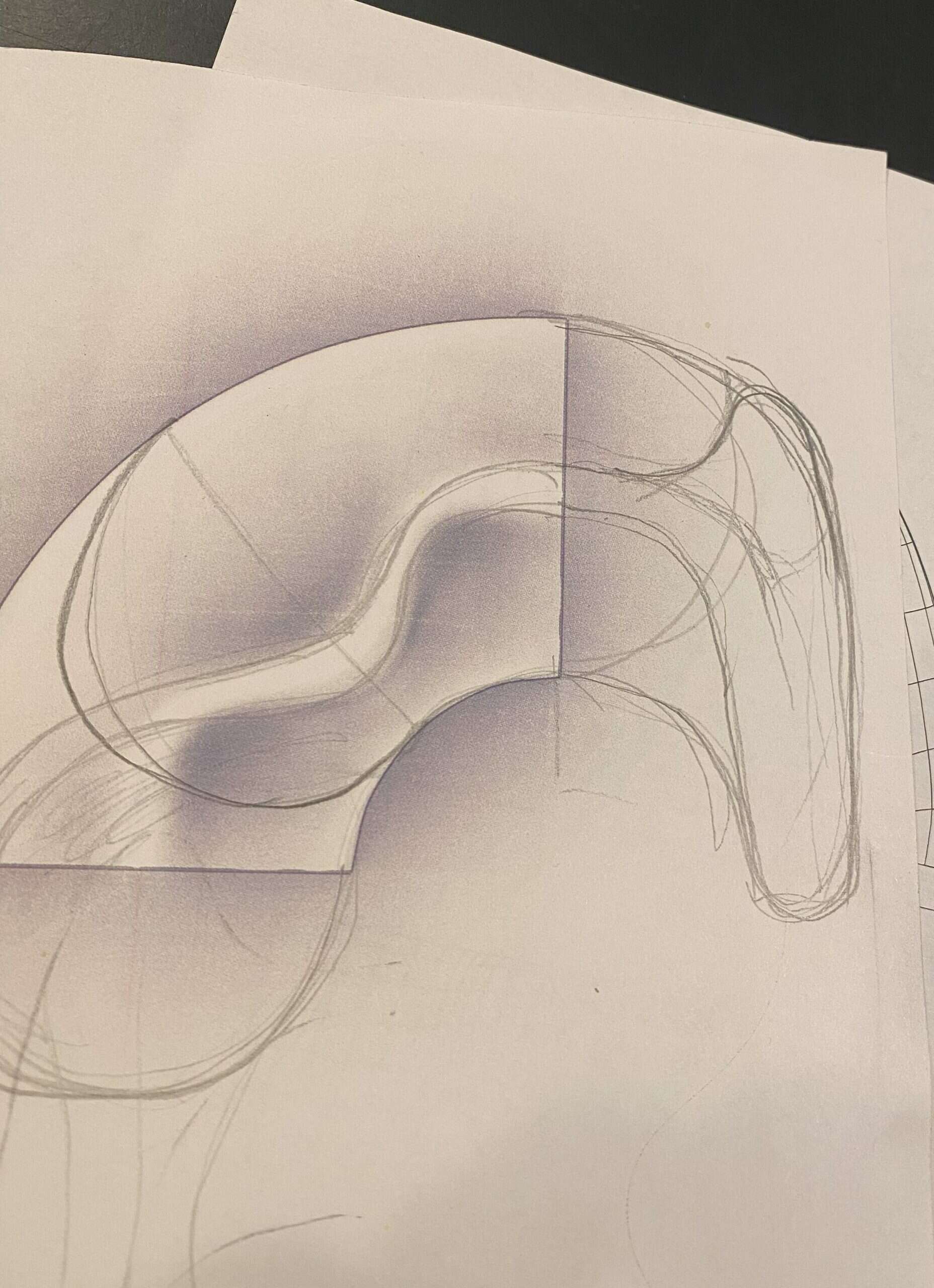
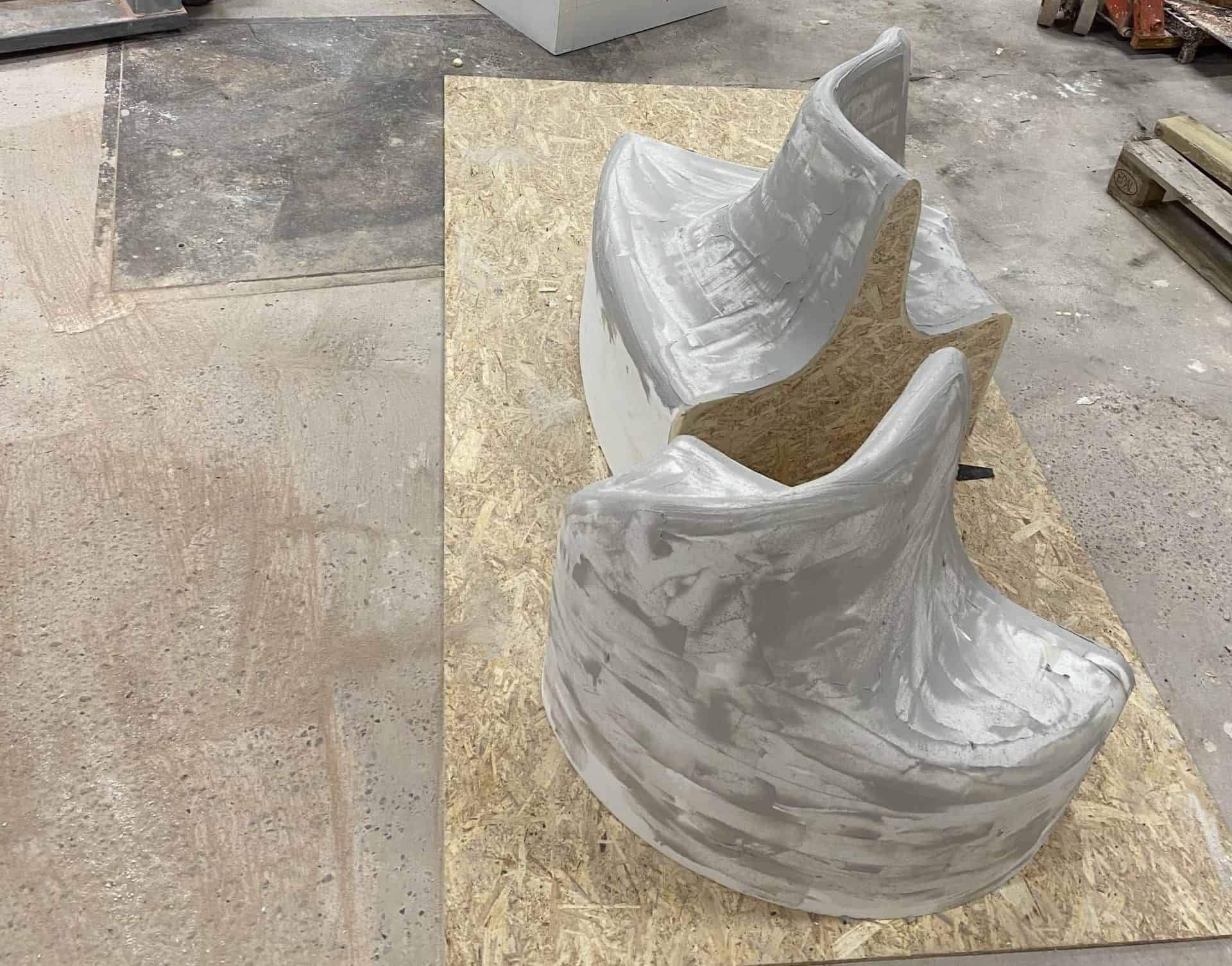
Dynamic flexibility
Initially, Troels thought he would use Målbar’s climate screening tool a lot more than he has. But he found the workshop hosted by Målbar interesting and has had a close collaboration with Målbar during his design process, resulting in a new approach to the hidden structural part of the modules made from paper pulp instead of wood. He sees a great potential of implementing the tool in the design of more commercial products, but usually Troels creates unique sculptural pieces on a much smaller scale.
The tool is an inspiring starting point, and I can imagine that it is well suited for measuring industrially produced products. My reduction focus has been on two things: creating a dynamic and flexible design that can be modified for changing needs. And on using this innovative coating material to avoid using virgin textiles for the cover.”
Troels thinks that this new way of coating is an attractive way to refurnish products when we grow tired of them. Lots of furniture is disposed of when it is worn, but spray coating a new textile surface on your sofa provides a different opportunity to renew our stuff.
Puts his own mark on
The fact that he cannot communicate with his client is not bothering Troels. However, he would have appreciated an opportunity to access information about their production methods, leftover materials, etc., to be able to tap into the client’s existing conditions. Since that hasn’t been possible, Troels have tried not to think about the client too much.
“When I cannot speak with them, I might as well focus on my own process and how I can incorporate my values into this task. I try to fulfill the most important parts of the brief, but I have also allowed myself to unfold my creativity. I feel I have created an unpretentious piece of furniture that is dynamic and flexible. It has been interesting to solve this task with so many parameters that needed to come together.”
This article reflects the designer’s own opinion and Målbar does not necessarily agree with their statements about materials, processes, etc.
Climate calculations and insights
Troels’ modular sofa coated with recycled textile spray is named Symmetry Sofa. 3 modules has an estimated climate footprint of 145 kg of CO2eq.
The choice of a flocked textile surface of recycled jeans has shown a nice reduction. If a woven virgin cotton textile had been selected instead, the emissions would be around 25% higher.
The design idea is using an interior supporting structure of molded recycled paper pulp modules. This novel choice of construction material provides significant reductions of the design.
42% of the total emissions comes from the use of molded foam. Therefore, it would be beneficial to put the focus here for further reductions in a continuous development phase.
Using the technology of coating the sofa modules with a flocked fiber surface instead of a traditional textile cover is quite new. And the flocking supplier has not been able to prove that the surface has the needed high wear resistance.
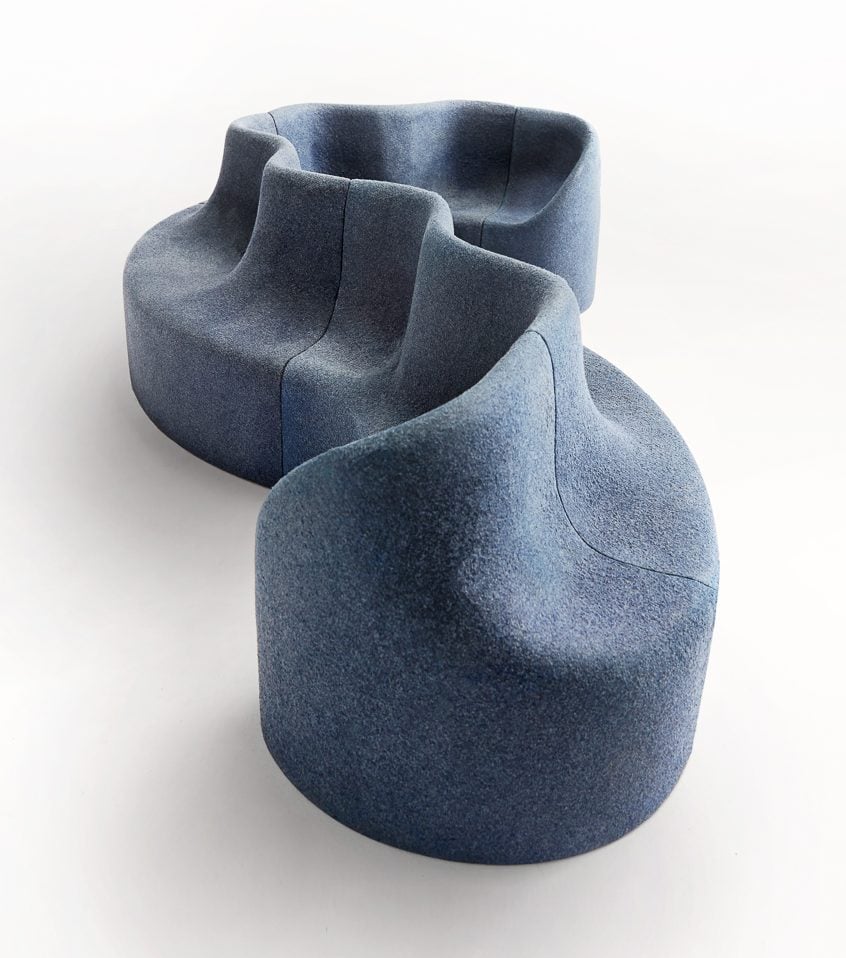
Photo by Kristine Funch
Climate bar explainer
The climate bar shows how the emissions from the design are distributed between 10 sources within the product life cycle. Here you can see that the biggest part of the climate footprint stems from the 7 kilograms of upholstery materials, which constitute 42% of the climate emissions. Meanwhile, the paper pulp used weighs 25 kilograms but only accounts for 36% of the footprint. Finally, it is noticeable that the textile surface only accounts for 6% of the footprint – since textiles usually constitutes a much larger part of an upholstered piece of furniture.
There are emissions from the use phase on all products, because of the waste that is generated from returned products from consumers.
Assumptions
- The amount of waste during spray gluing and flocking is based on reported amounts from the supplier.
- The amount of PU molding waste is estimated to 10% of the finished molded foam.
- The amount of pulp molding waste is estimated to 40% of the finished items.
- The emissions of recycled jeans fibers are based on a calculation of average emissions from indigo dyed cotton jeans based on EU’s Draft PEFCR for Apparel.
- We assume that metals, plastics, and textiles are produced according to the global average unless we know differently. All other materials are assumed to be produced in the EU
- We assume a transport distance by lorry from supplier to warehouse of 1,000 km
- We assume a transport distance from warehouse to final client of 1,000 km
Målbar builds their assumptions on their experience with industrial production and LCA’s on manufacturing companies.
Context
Målbar participates in Danish Design Makers’ 2024 design challenge, The Blind Date experiment where 19 designers and design duos answer furniture briefs from anonymous European furniture companies. The designers use Målbar’s climate screening tool to gain insigths into the climate emissions of materials and production processes, learning about the climate impact of their design choices. Ultimately, the total climate footprint of each design will be calculated and presented at ORGATEC in Cologne on October 22nd-25th 2024.