Gudmundur Ludvik,
furniture designer
Gudmundur Ludvik Gretarsson moved from Iceland to Denmark where he completed his formal education as a furniture designer at the Danish Design School in 2002. He runs his own studio, based in Vejle and has been a member of Danish Design Makers for 10 years.
The next position is the best
Gudmundur thinks the brief he received fits well into his way of working. He sees many opportunities and interesting challenges in it and likes the technical aspects along with the focus on mobility.
“I enjoy the technical aspect of the process, and I like my designs to be interactive, to be able to change or transform in order to fulfill the desired function. I thought; either the furniture can be mobile or the person using it can be mobile. I have chosen to create a sit-and-stand furniture piece for in between areas that promotes movement. It is not a lounge sofa that you sit in for hours. Rather, it is a component that supports you on your way to something. That gives you a break or a short rest.”
Gudmundur is building a piece of furniture that consists of four differently shaped cylindrical modules that can be put together in various ways for various needs. It will be an element that can change expression and shape as often as wanted, to follow changing needs, and taste, in order to prolong its lifetime.
It all started with this mechanism, a click system, for assembling modules in an intuitive and simple way. It enables the modules to be connected in different angles, while the legs serve as the lock. I like to explore and learn new things. And I like to be challenged on my technical skills and to create customizable designs. This project has been that kind of a challenge.”
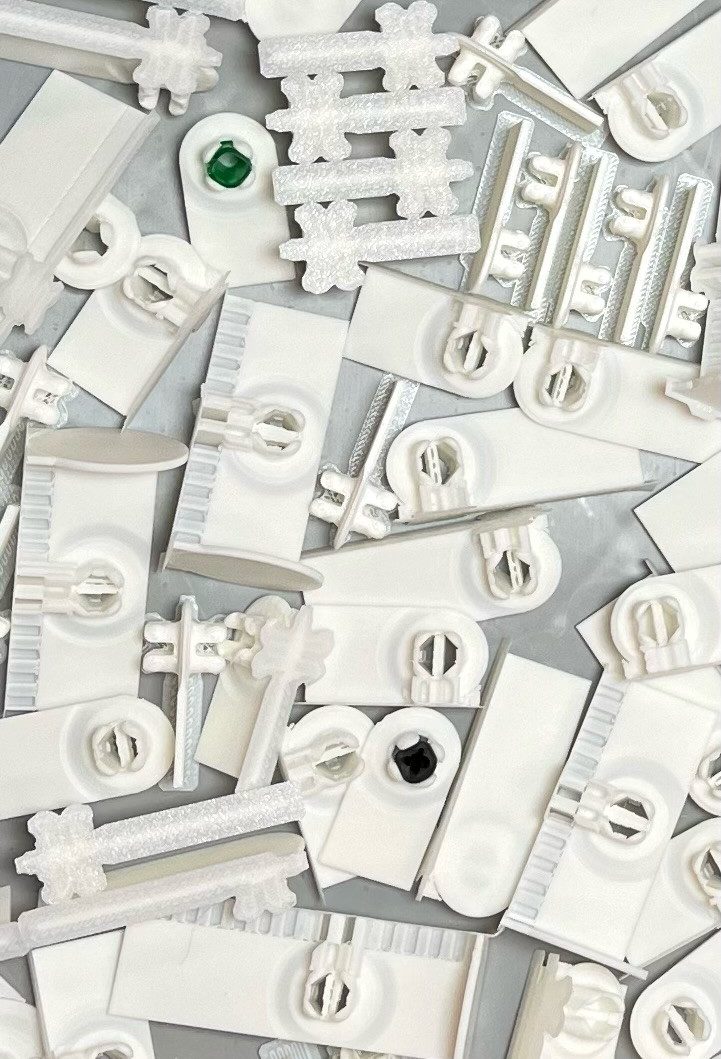

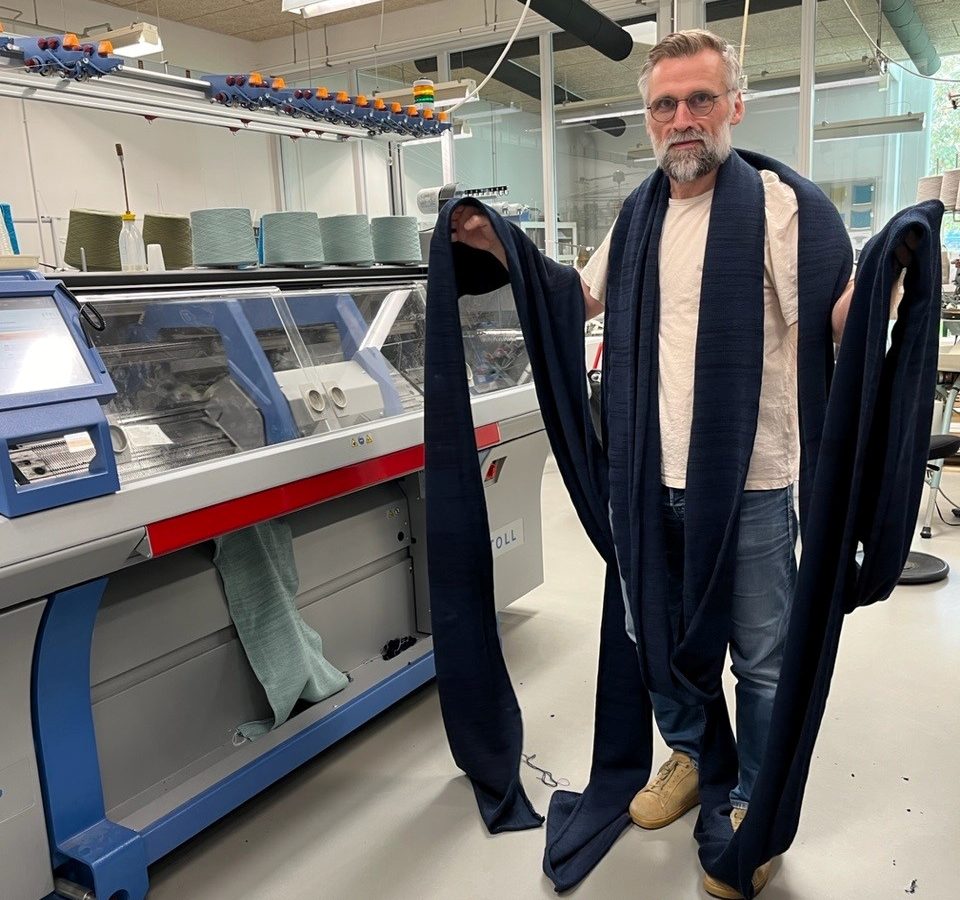
Increasing the chance of life-long attractiveness
By choosing cylinder shaped elements for the carrying construction, Gudmundur has made it possible for the upholstery parts to be pulled onto the base. Together with his choice of using knitted textile, he avoids stitches and enables yet another transformation of his design. Because when the textile is worn, it can be rotated, so that the unused sides come on top and into use. The inner structure of the modules is made of molded pulp tubes providing the design with a strong construction in a low emitting material.
To me, it makes sense to design for disassembly. I like to know that the different parts of my product can be reused or recycled. It is designed to be produced from existing recycled material flows such as post-consumer and bio-based foam. But even more, it is essential to me that my design is able to change and be modified to stay attractive and relevant to the users for a long time.”
Målbar’s climate screening tool has supported Gudmundur in his design process. He has used it to illustrate different scenarios with various materials and processes. However, he also finds it challenging sometimes that the tool doesn’t consider some of the softer parameters that are important to him. Like the possibility of transforming a design.
Well-functioning design is automatically appealing
Gudmundur prioritizes function above all other parameters, and he believes it is closely connected to the sustainable aspect which again is closely connected to durability. In the end, he just wants everything to come together.
“In my experience, when designing you are faced with several and closely linked challenges, such as constructional issues, pricing, aesthetic preferences, and environmental impact. Good solutions add value across all these parameters at the same time. To me, sustainability is when it all adds up, in perfect balance.”
This article reflects the designer’s own opinion and Målbar does not necessarily agree with their statements about materials, processes, etc.
Climate calculations and insights
Gudmundur’s furniture group is called KRYB which means creepy-crawly in Danish.
All modules have a total estimated climate emission of 650 kg of CO2eq.
The main part of KRYB furniture’s emissions originates from the wool textile fiber. Wool fiber production has a very large footprint because of sheep’s methane emissions.
Gudmundur has added a minimum amount of foam to his design. This has a positive effect on the climate impact, but it seems small in comparison to the high emissions from textile.
The transport emissions are quite high because of the choice of only one size of cardboard box which results in a larger volume than needed for the 8 modules displayed. This can be optimized for a reduced climate footprint.
The footprint of the furniture can be reduced significantly by selecting alternative textile fibers and more compact packaging.
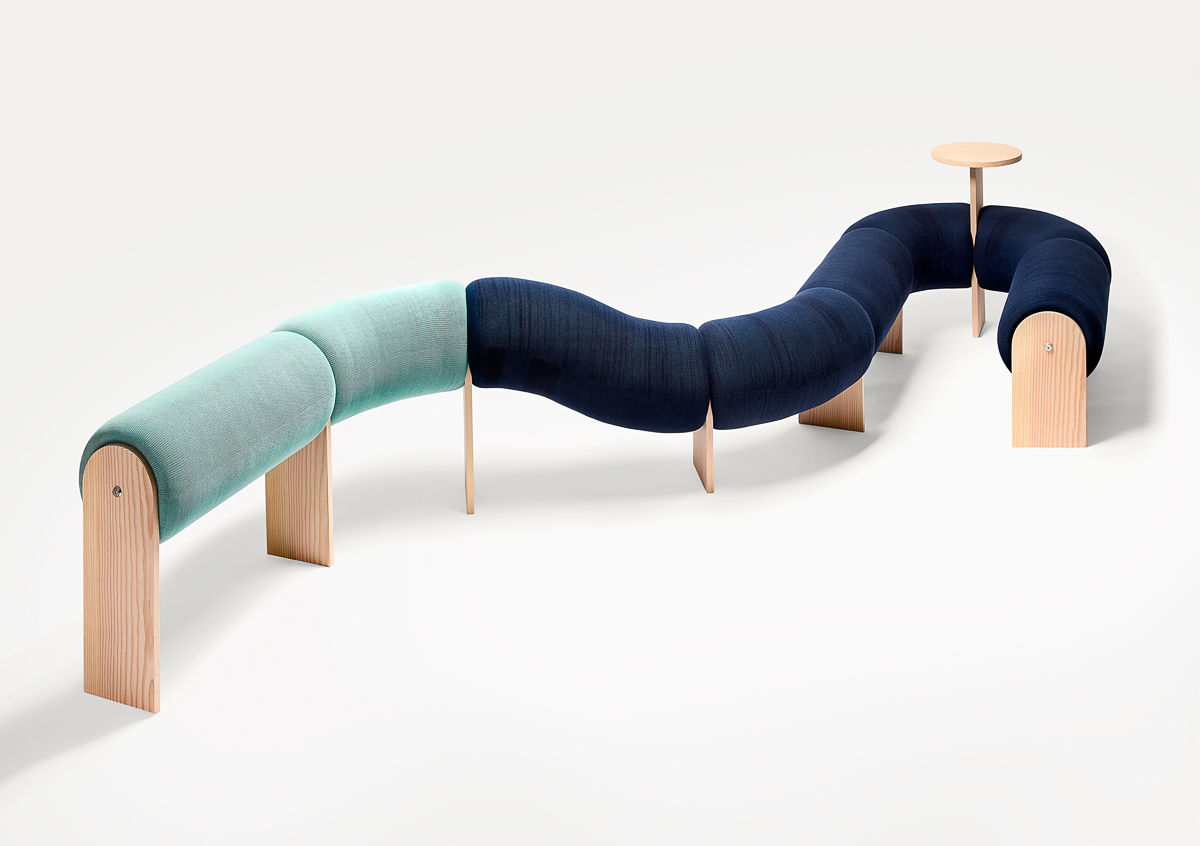
Photo by Kristine Funch
Explanation of climate bar
The climate bar shows how the emissions from the design are distributed between 10 sources within the product life cycle. Here you can see that the largest part of the emissions comes from the textile cover and textile waste. In the spinning process of wool, a large amount of fiber is often wasted because the fibers are too short or too curly to be spun. Finally, it is worth noting that when spraying on surface treatment, it typically results in a large amount of waste. Hence the surface finish also holds a noticeable share of the total climate impact.
There are emissions from the use phase on all products, because of the waste that is generated from returned products from consumers.
Assumptions
- Surface treatment spray waste is set to 50%
- Solid wood manufacturing waste is set equivalent to the amount of wood used
- Pulp molding is assumed dried with bio heat or by natural air drying.
- We assume that molded plywood generates 30% of manufacturing waste based on its shape.
- Block foam waste is set to 15% and the knitted textile tube waste is set to only 10%
- We assume that metals, plastics, and textiles are produced according to the global average unless we know differently. All other materials are assumed to be produced in the EU
- We assume a transport distance by lorry from supplier to warehouse of 1,000 km
- We assume a transport distance from warehouse to final client of 1,000 km
Målbar builds their assumptions on their experience with industrial production and LCA’s on manufacturing companies.
Context
Målbar participates in Danish Design Makers’ 2024 design challenge, The Blind Date experiment where 19 designers and design duos answer furniture briefs from anonymous European furniture companies. The designers use Målbar’s climate screening tool to gain insigths into the climate emissions of materials and production processes, learning about the climate impact of their design choices. Ultimately, the total climate footprint of each design will be calculated and presented at ORGATEC in Cologne on October 22nd-25th 2024.