Nikolaj Steenfatt, product and furniture designer
Nikolaj Steenfatt is a young and experienced furniture and product designer, educated from the Royal Danish Academy of Fine Arts, School of Design in 2013, and he is a board member of Danish Design Makers.
Minimalism over experimenting
Nikolaj is designing a lighting product, where he focuses on minimalism. This is because the electric parts are mandatory and thus the additional material must be able to sustain the heat and light.
My solution in this project is to create a simple product where material consumption and number of elements are minimized. I want it to be flat-packed and it is also designed for disassembly.”
With his design, Nikolaj is working to create a calming and balancing effect in the room, and he wants the product to have a sculptural purpose.
To reduce the impact of his design, Nikolaj has chosen to work with only two materials – besides the electric parts – that are recyclable and that can be made very slim.
Changing the industry
But Nikolaj’s work with reduction expands beyond the product. He has designed the product measurements to be flat packed in cardboard boxes that fit the measurements of standard euro pallets. Furthermore, he has selected materials that do not need much processing to gain the visual expression and functions, he wants.
“To me, it is not only about choosing more responsible materials but also efficient production techniques. If we wish to make an impact on the green agenda, we must design products that sell. And for a product to sell, it needs to be profitable for the company who sells it, meaning it must not be too expensive. As a designer, you cannot ignore this”
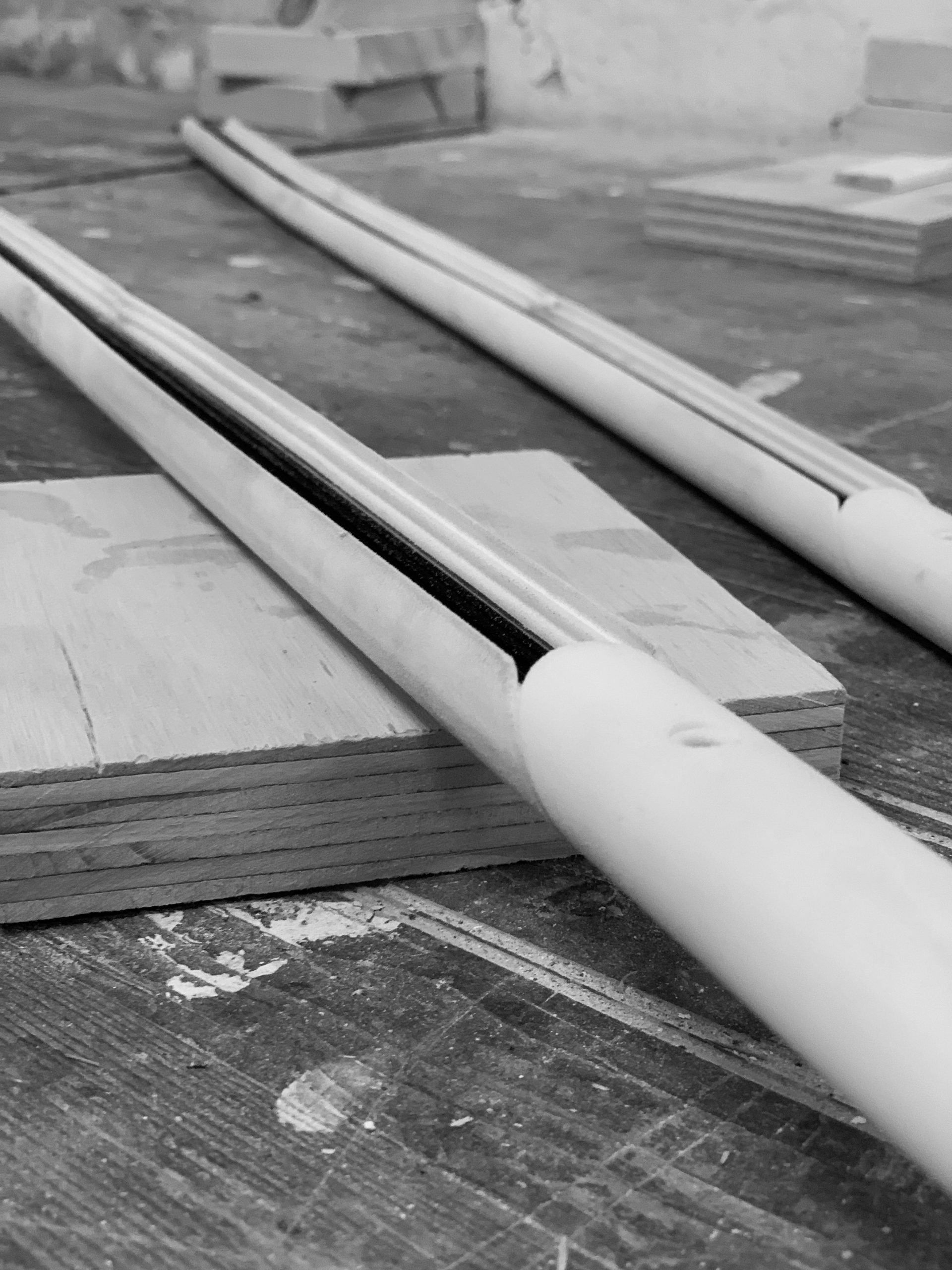
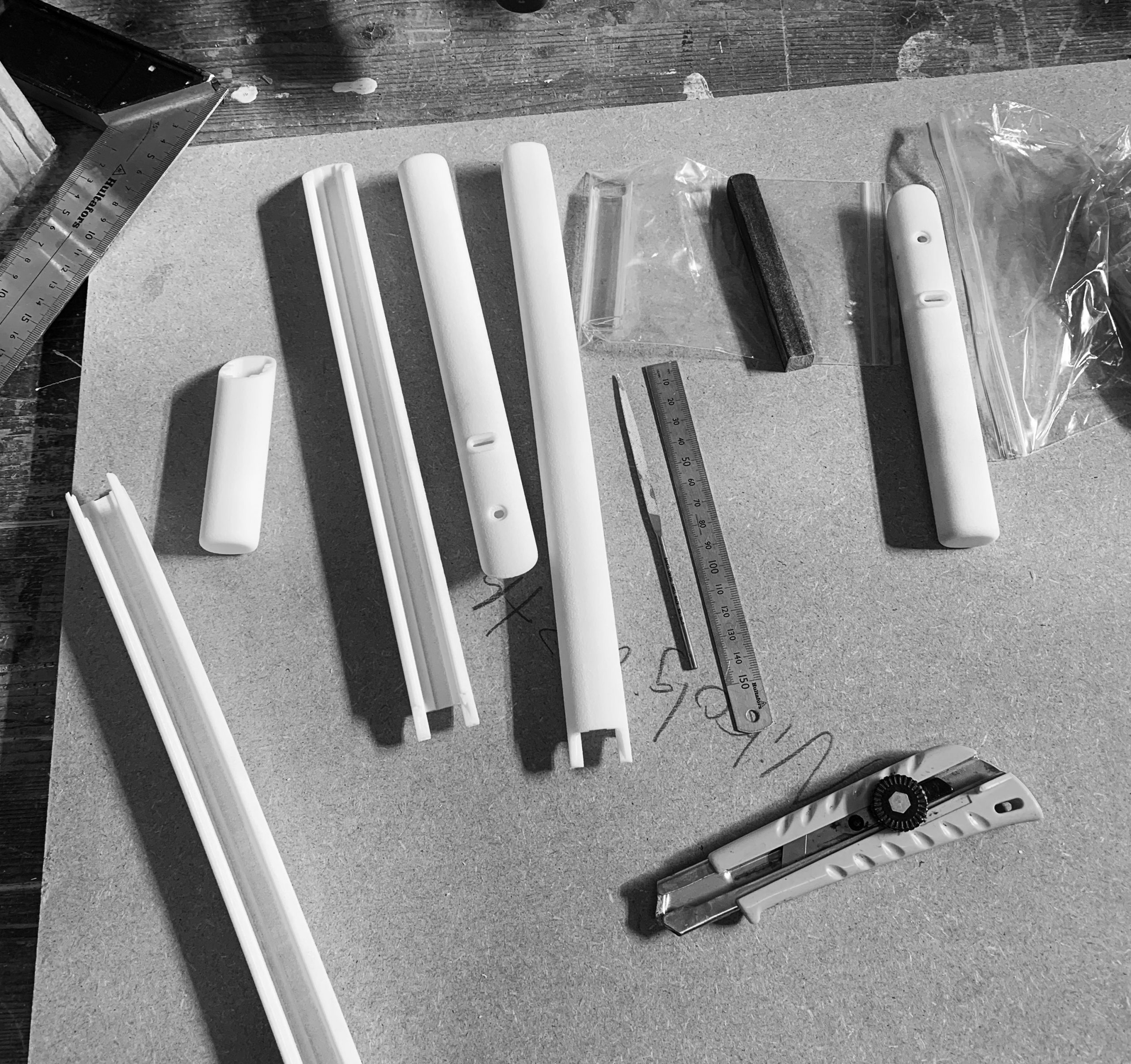
Nikolaj thinks that designers are capable of putting some pressure on the manufacturers and of designing in a certain direction. And he does encounter a will amongst manufacturers to take a more responsible approach. According to Nikolaj, the production techniques might be one way forward.
As a designer, I cannot decide alone whether my designs will be made from virgin or recycled material, but I might be able to design for a visual expression that requires less processing and a specific production technique that requires less energy. And the more material-oriented we make our designs, the greater the chance that the manufacturers will follow our wishes. It takes two to make the right decisions.”
Nikolaj’s focus has first and foremost been on developing a durable concept, thus he hasn’t used the Målbar tool very much at the beginning of his design process. Nevertheless, it has been at the back of his mind the whole time and he feels that the cooperation with Målbar in general has influenced his design approach and made him work very seriously with the reduction theme.
“I think reduction of environmental impact should be part of all new designs”
This article reflects the designer’s own opinion and Målbar does not necessarily agree with their statements about materials, processes, etc.
Climate calculations and insights
Nikolaj has named his lamp AERO and he has designed a small and a large version of it.
The small one has an estimated climate impact of 75 kilos of CO2eq.
The big version has a total estimated climate impact of 110 kilos of CO2eq.
The major part of the lamp’s climate footprint comes from the energy consumed in the use phase. The emissions from the use phase can be reduced further by choosing a less energy consuming light source.
The second largest footprint comes from the aluminum parts. These could be effectively reduced by using low emission aluminum, that is aluminum manufactured with renewable energy, or alternative construction materials.
Nikolaj’s attempt to reduce the footprint by making the metal materials accessible for recycling at end of life has effectively reduced the total emissions by 8%.
Even though Nikolaj has designed all parts for disassembly, the other recyclable materials, such as the plastic parts, are not expected to be recycled at the end of life with the current EU recycling scenario. However, this will hopefully change for the better in the future, so Målbar still encourages designers to design all parts for disassembly.
Flatpacking the product does reduce transport emissions. But for a single product, it doesn’t make an obvious impact, since the transport constitutes only a small part of the total climate footprint.
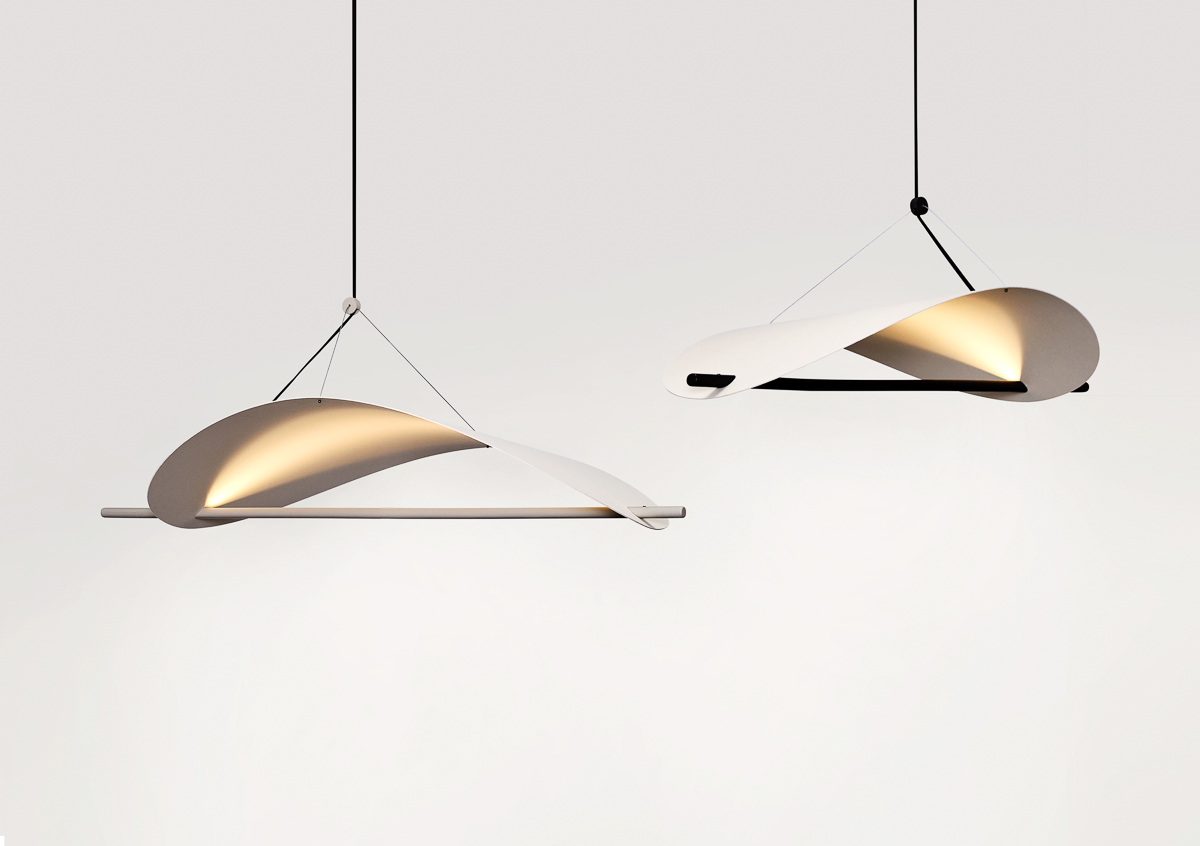
Photo by Kristine Funch
Explanation of climate bar
The climate bar shows how the emissions from the design are distributed between 10 sources within the product life cycle. Here you can see that a major part of the footprint comes from the product use phase. Next, the materials – in this case the aluminum parts – constitute the second largest part of the climate bar. You can also see that a part of the bar lies below zero. This illustrates the credit given for recycling the metal parts at end-of-life made possible by the design for disassembly.
Assumptions
- We assume 5% waste for the manufacturing of a metal profile
- For the aluminum shade, an average 25% of manufacturing waste is added because the oval shape creates more waste in comparison to the rectangular raw sheet.
- A standard EU 1000 hours per year energy consumption has been added during the 15 years of expected product life time.
- We assume that metals, plastics, and textiles are produced according to the global average unless we know differently. All other materials are assumed to be produced in the EU
- We assume a transport distance by lorry from supplier to warehouse of 1,000 km
- We assume a transport distance from warehouse to final client of 1,000 km
Målbar builds their assumptions on their experience with industrial production and LCA’s on manufacturing companies.
Context
Målbar participates in Danish Design Makers’ 2024 design challenge, The Blind Date experiment where 19 designers and design duos answer furniture briefs from anonymous European furniture companies. The designers use Målbar’s climate screening tool to gain insigths into the climate emissions of materials and production processes, learning about the climate impact of their design choices. Ultimately, the total climate footprint of each design will be calculated and presented at ORGATEC in Cologne on October 22nd-25th 2024.