Thomas E. Alken,
furniture designer
Thomas runs his own renowned design studio called Format Design and he is a board member in Danish Design Makers.
I want people to think
“Wow, can I be this comfortable in so little?”
Thomas E. Alken is happy about his very comprehensive and detailed brief because of the opportunity to design and create a cool seating object for a tough contract market. He hasn’t designed a lot for the indoor contract market before, so this is a challenge, but also what makes the brief interesting.
The company seems very conscious about who they are, what they want, and don’t want. I hope to make them happy with my design”.
Thomas has managed to design several variations of his product in a very short time. And he has thought about every little detail of all the functions he wants it to have. He considers how different people and age groups will use it, he thinks about how it can be moved when cleaning, and he has ensured users’ private space in an elegant way.
Furniture made for the contract market must live up to high durability, stability, and safety standards, which makes the reduction part another challenge. Thomas works his way around this by not compromising too much on the amount of material that goes into his design but rather he puts his focus on optimizing the use of the standardized measurements of the materials to minimize waste and left over materials.
He also works with an alternative to upholstery and considers in detail how he can create high comfort without using the traditional upholstery materials.
“Comfort is really important to me, so if I can make a comfortable product without foam and glue, I have succeeded”.
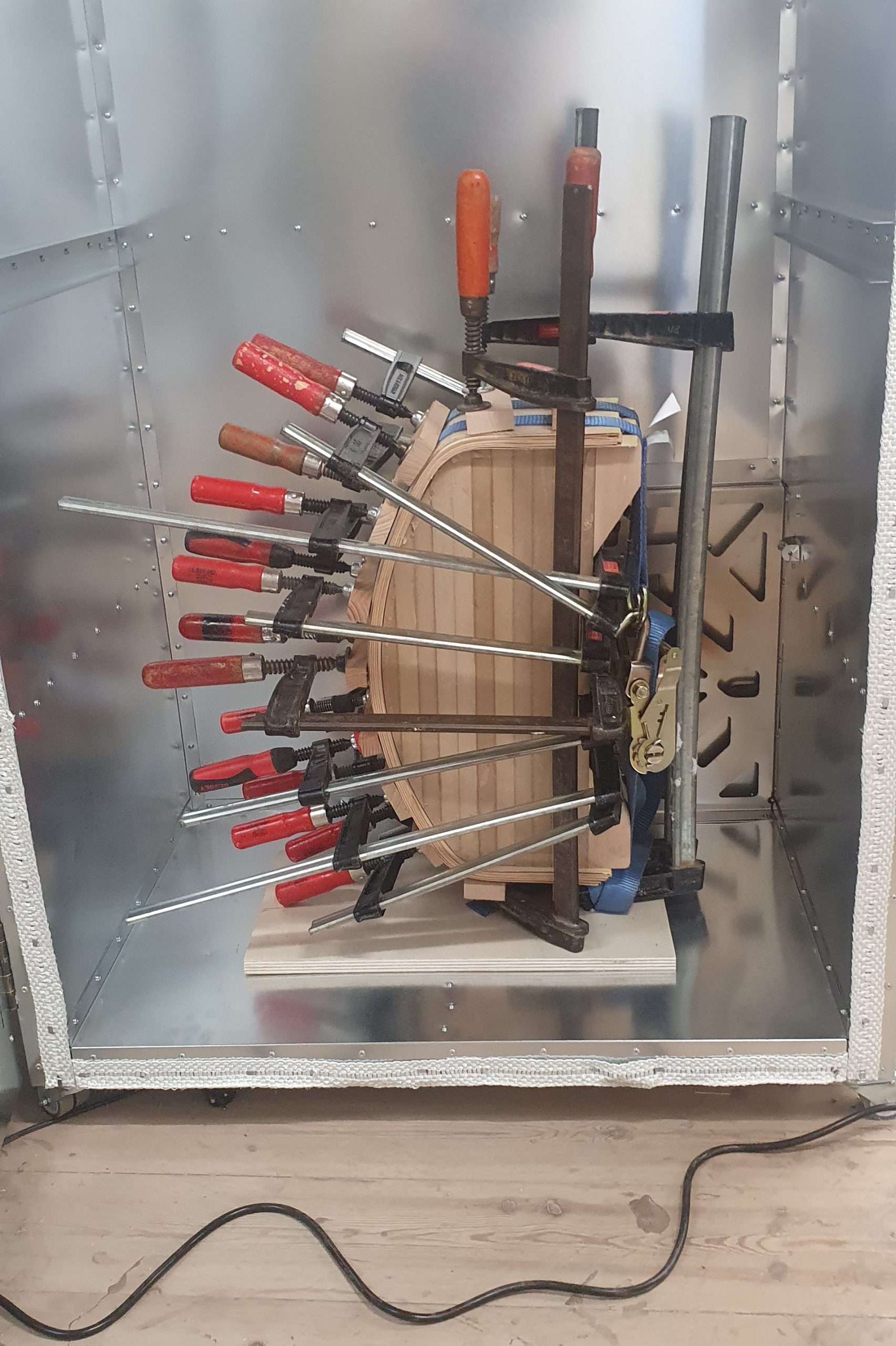
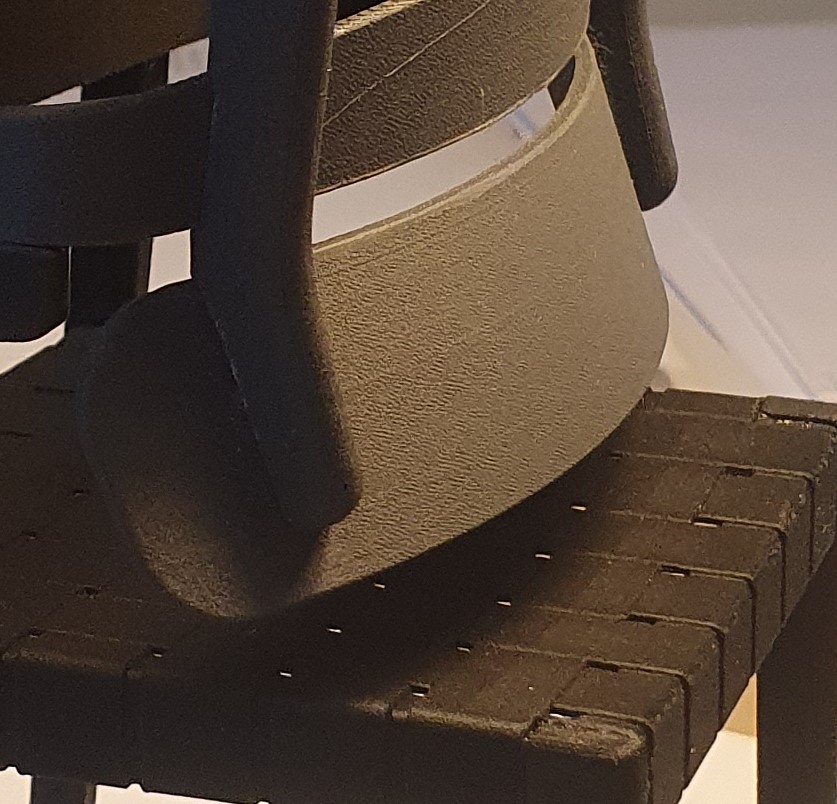
Balancing climate knowledge and creative expression
Thomas thinks that the Målbar climate screening tool is very useful and important.
“As a designer, you might have all kinds of ideas and assumptions about the climate impact of different materials and processes, but often you do not have anything to pin it on. We get that in Målbar’s tool. Prove or disprove of our conjectures”.
On the other hand, as an Associate lector at the Royal Danish Academy of Design, Thomas also experiences that some design students are somewhat paralyzed by their knowledge about the environmental impact of materials and production. Some don’t even allow themselves to use specific materials on modeling level. This is a balance that can be difficult for some to master.
I like the idea of using Målbar’s tool in schools, but it must not restrict or limit the room for expressing creativity. I fear that the new generation of designers will be too afraid to do anything if they do not realize that the creative process requires us to use some materials. If we do not experiment with different materials, shapes, and techniques, we won’t be able to design products that have a place in world. The main part of the climate impact of a product is determined in the design phase but stems not from the materials we use for modelling. When we succeed in making less emitting designs, the modeling material we have used aren’t wasted”.
From Målbar’s perspective, it is positive that many design students are aware of their climate footprint even in their design process. But it is sure a challenge if it prevents some from unfolding their creative process and fulfilling their potential as environmentally responsible designers.
Målbar always tries to stay updated on new, promising materials and production techniques, because it is part of the solution to find better ways of producing the goods that we need.
This article reflects the designer’s own opinion and Målbar does not necessarily agree with their statements about materials, processes, etc.
Climate calculations and insights
Thomas’ has designed two versions of his dining chair; TEA01 with armrest and woven strap weaving for seat and TEA02 without armrest with wood-based seat and painted with black lacquer.
The one with seat-webbing has an estimated total climate impact of 28 kg of CO2eq.
The painted version has an estimated total climate impact of 25 kg of CO2eq.
The strategy of reducing material waste from manufacturing results in significant reductions on the webbing textiles, but not so much on the wood. This is because among the selected materials in this design, only the textile materials generally have high emissions.
The attempt to avoid emissions from upholstery foam has only a little positive effect because the amount of upholstery foam needed for this design would be low.
The choice of recycled polypropylene for the straps leads to lower emissions, but the reduction is only 3% as most of the emissions from textiles come from the electricity consumption during production.
The chair has potential for further reductions by choosing a self-supporting upholstery textile which is lighter and with a more open weaving.
As for the painted chair, the strategy of reducing material waste from manufacturing of solid wood results in a 4% reduction. Wooden materials in general have low emissions.
The choice of lacquering by wet spraying an open chair frame results in a high amount of lacquer waste. Hence the emissions from surface treatment could be reduced by 8% by replacing the wet spray lacquering with a powder coating of wood.
The emissions from the painted chair can be further reduced by optimizing the molded plywood parts to lower thickness and weight.
For both versions of the chair, reductions in transport emissions can be obtained by designing the chair for flat packing.
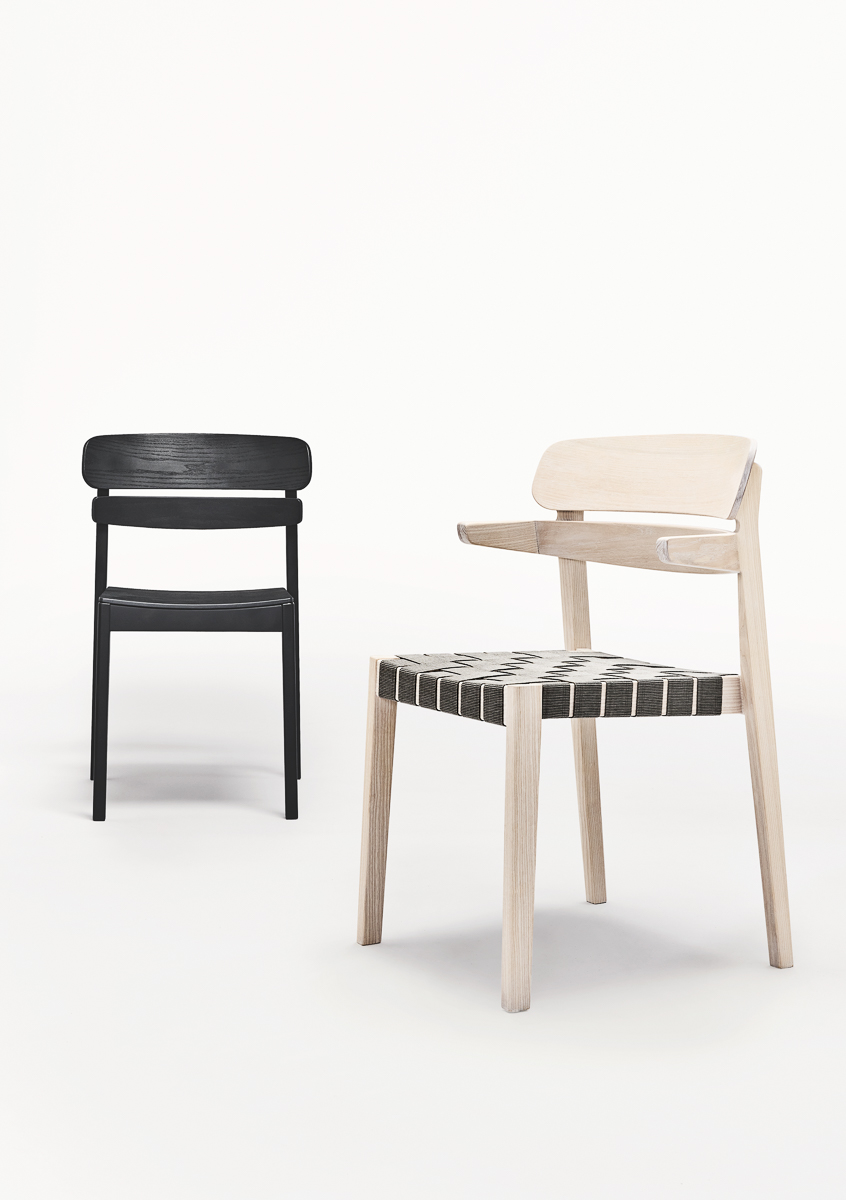
Photo by Kristine Funch
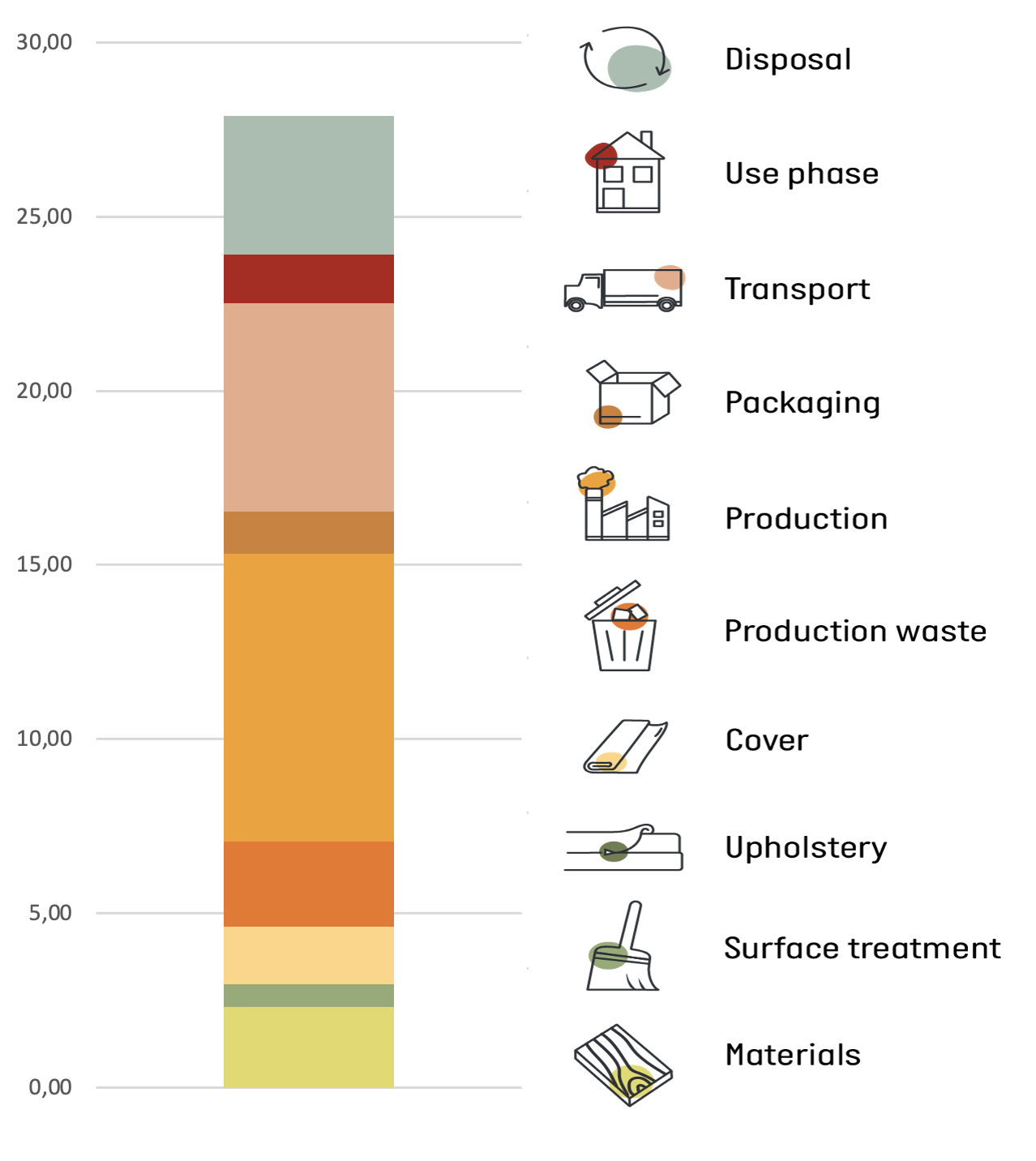
Målbar climate bar of TEA01, webbing chair
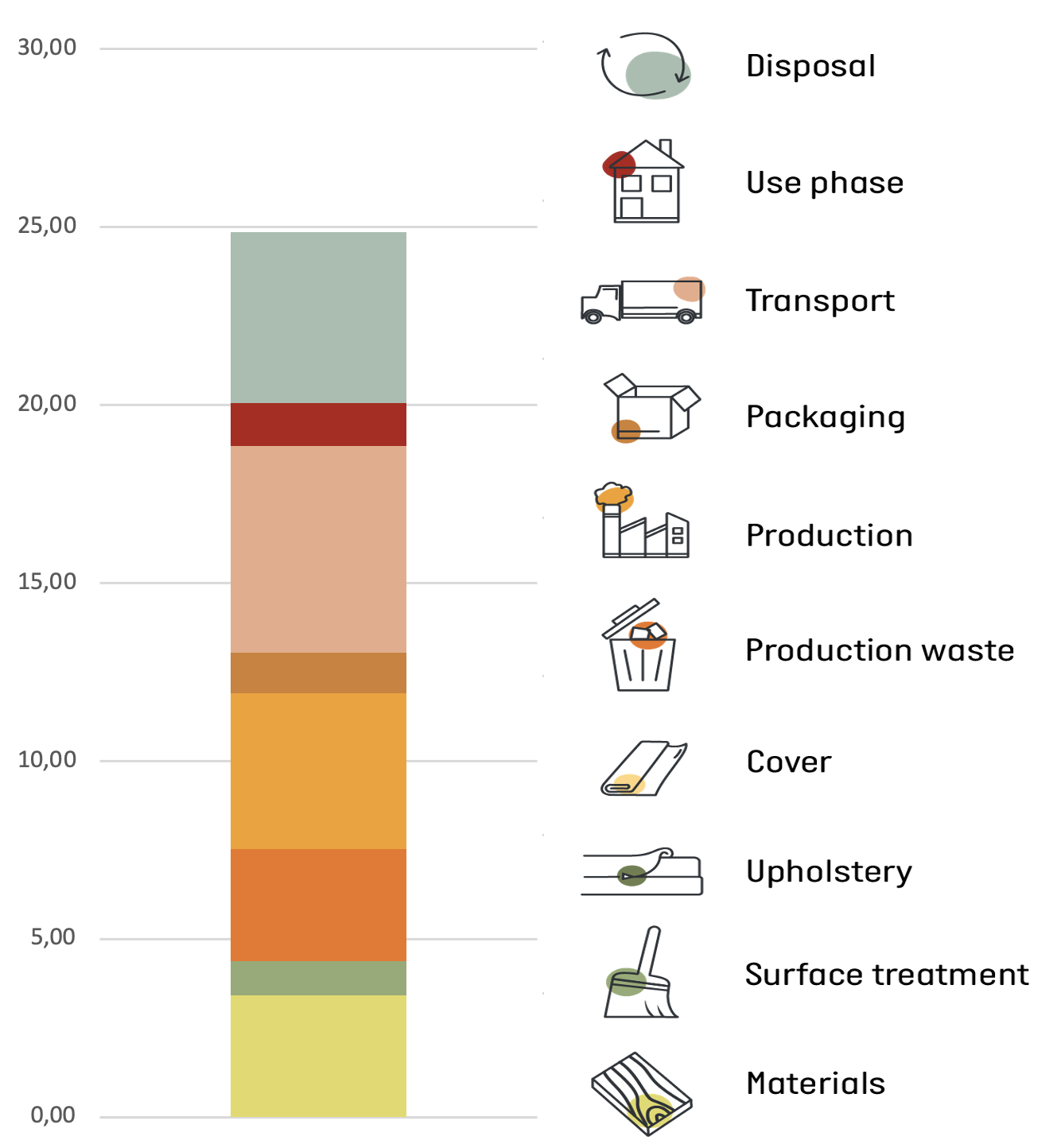
Målbar climate bar TEA02, painted chair
Explanation of climate bar – webbing and armrest version
The climate bar shows how the emissions from the design are distributed between 10 sources within the product life cycle. Here you can see that the largest part of the footprint stems from the production phase. This is mostly due to the manufacturing of the textile straps.
Also, transport takes up a significant part of the emissions. This is because a lot of air is carried when shipping large items that cannot be flat-packed, even though the transport emissions are lowered by the fact that the chair is stackable. We have estimated that four chairs are shipped together in a box.
Explanation of climate bar – painted version
In this version, the emissions are more equally divided between sources. But also here, transport carries a significant part of the footprint. Notably is the disposal phase, which constitutes almost 20% of the total climate footprint. This is due to the fact that the chair is only made of wood, and the biggest emissions from wood happen at end-of-life if the product is landfilled and composted since this has high methane emissions.
There are emissions from the use phase on all products, because of the waste that is generated from returned products from consumers.
Assumptions
- The molded plywood is assumed to have 30% cutting waste.
- We assume that metals, plastics, and textiles are produced according to the global average unless we know differently. All other materials are assumed to be produced in the EU
- We assume a transport distance by lorry from supplier to warehouse of 1,000 km
- We assume a transport distance from warehouse to final client of 1,000 km
Målbar builds their assumptions on their experience with industrial production and LCA’s on manufacturing companies.
Context
Målbar participates in Danish Design Makers’ 2024 design challenge, The Blind Date experiment where 19 designers and design duos answer furniture briefs from anonymous European furniture companies. The designers use Målbar’s climate screening tool to gain insigths into the climate emissions of materials and production processes, learning about the climate impact of their design choices. Ultimately, the total climate footprint of each design will be calculated and presented at ORGATEC in Cologne on October 22nd-25th 2024.